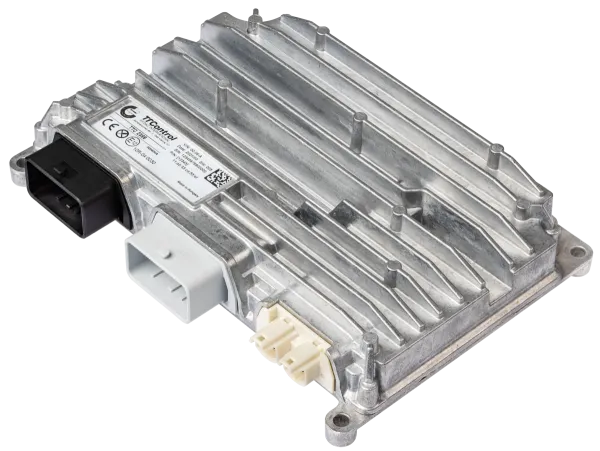
TTC 2300 Family
Powerful and scalable safety electronic control units for highly automated vehicles
The TTC 2300 family is the first member of a complete and scalable series of controllers designed to meet the needs of upcoming highly automated and smart vehicles.
Key Features
The TTC 2300 ECUs are equipped with the second generation high performance AurixTM TriCoreTM CPU, with up to six cores, each running at 300 MHz. Fulfilling highest security standards, the CPU is equipped with a Hardware Security Module.
The TTC 2300 family supports advanced data configuration, logging and storing, equipped with internal and external Flash memory and an efficient efficient memory management and data transfer system.
The TTC 2300 variants are equipped with up to 60 inputs and outputs (I/O). The I/Os are highly configurable and can be flexibly configured for different types of sensors and actuators, which helps to save time and development costs.
Four CAN-FD interfaces with up to two Mbit/s and are equipped with two high-speed data (HSD) connectors for Ethernet and BroadR-Reach communication. These provide the necessary bandwidth for the increasing number of sensor and actuator data in vehicles.
TTC 2300 is ASIL C safety certified for cars, trucks, and buses (ISO 26262) and offers a mixed criticality concept allowing both safety-related and non-safety-related code to be executed on the same CPU without reducing the overall safety level.
The TTC 2300 product family is delivered with the safety-certified, real-time operating system PXROS.
For the TTC 2300 family, the H-Bridge interface offers the possibility of controlling electric motors providing an interface that supports frequencies up to 1 kHz and currents up to 4A.
We provide off-the-shelf electronic control units and displays to accelerate time-to-market in vehicle development.
Resources
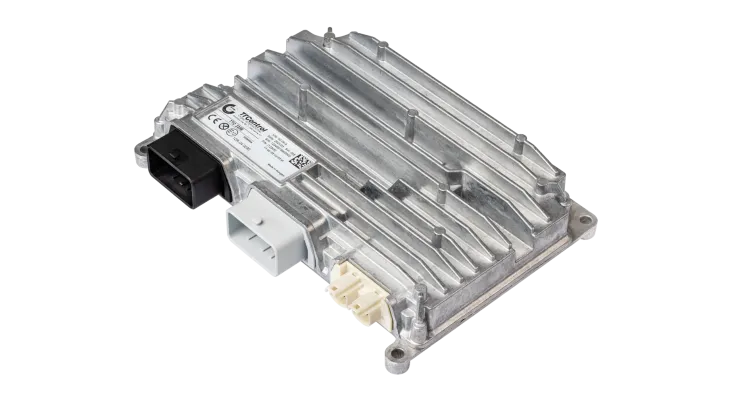
Learn more
If you have any questions about the TTC 2300 Family, don't hesitate to reach out to us.